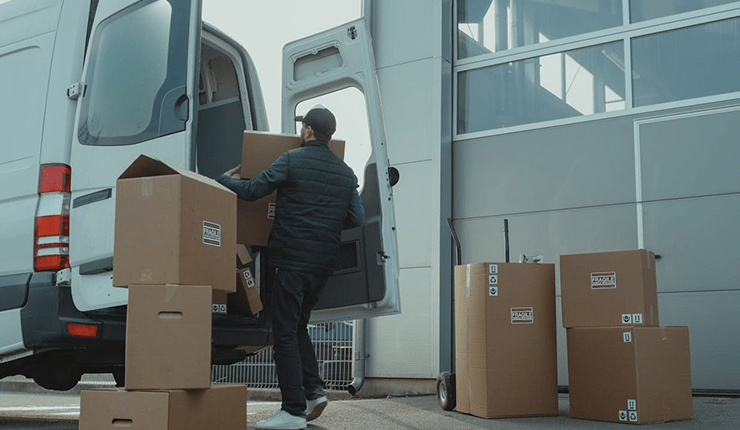
The Hidden Costs of Delayed Deliveries
How Proactive Logistics Saves Your Business Time and Money
A late delivery is more than just an inconvenience — it can have serious financial and reputational consequences. For businesses, especially those dealing with retail, manufacturing, or perishable goods, timely delivery is critical. Every delayed shipment can trigger a chain reaction of issues: dissatisfied customers, lost sales, production delays, and additional expenses for expedited shipping or customer appeasement.
The hidden costs of delayed deliveries are often overlooked. They include increased customer service demands, damage to brand reputation, reduced customer loyalty, and potential contractual penalties. For B2B relationships, a single missed deadline can jeopardize future partnerships or long-term contracts.
Proactive logistics is the key to avoiding these costly pitfalls. This approach involves anticipating potential disruptions, planning flexible routes, maintaining strong communication channels, and using data to improve decision-making. Technologies such as GPS tracking, automated alerts, and warehouse management systems help identify issues early and allow for rapid responses.
By investing in proactive logistics, companies can significantly reduce risk and enhance performance. They gain better control over their supply chain, improve customer satisfaction, and protect their bottom line. In today’s competitive landscape, the cost of being reactive is simply too high.